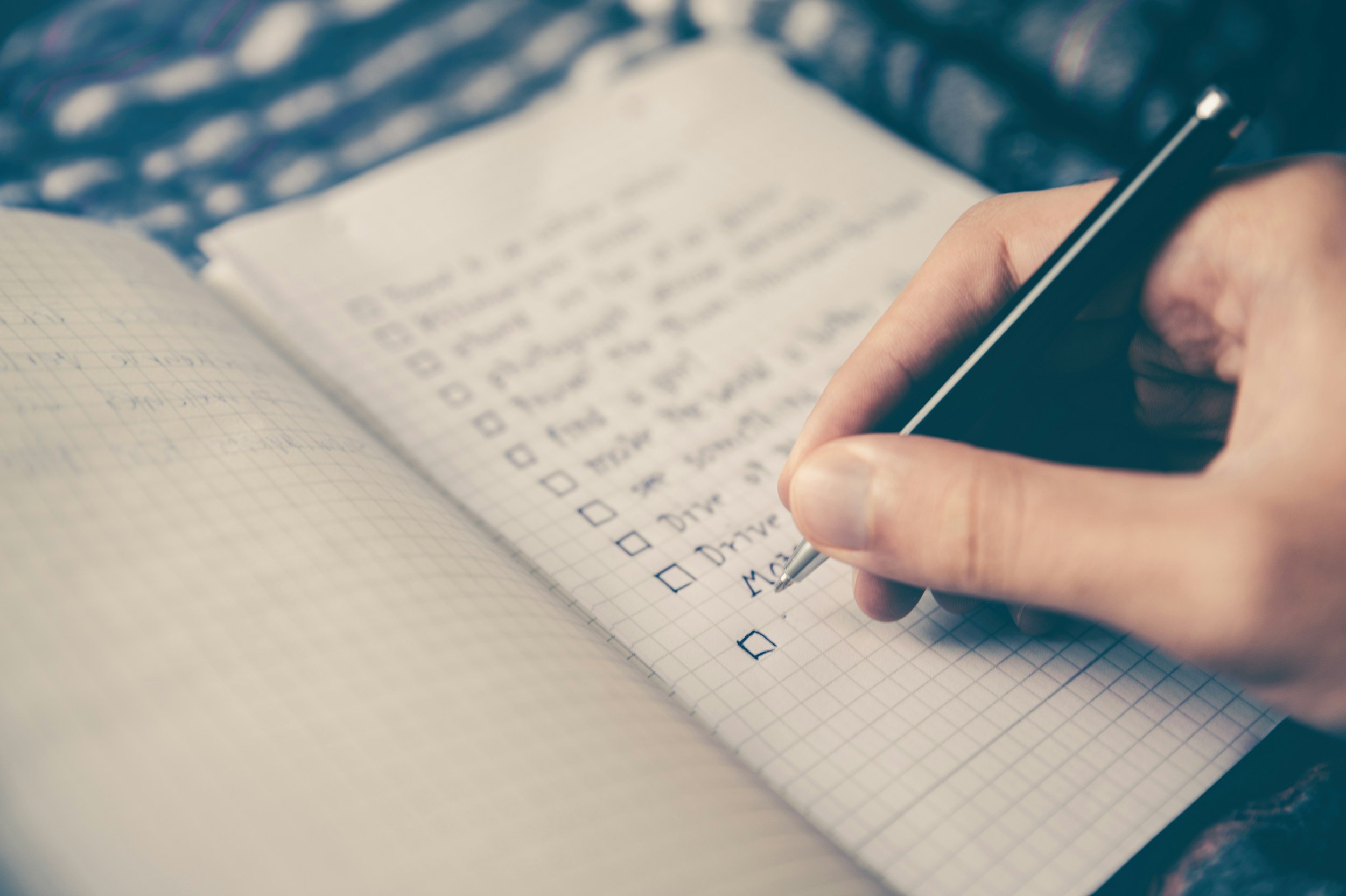
Failure Mode & Effects Analysis (FMEA)
Failure Modes and Effects Analysis (FMEA): Proactively Managing Risks
Why FMEA Matters
In today’s competitive landscape, risk management is not just a safeguard—it’s a strategic advantage. Failure Modes and Effects Analysis (FMEA) is a systematic approach to identifying and mitigating potential failures before they occur, ensuring robust processes and high-quality products. By mastering FMEA, organizations can:
Prevent Costly Failures: Address potential issues proactively, avoiding expensive rework, recalls, or customer dissatisfaction.
Enhance Product and Process Reliability: Build confidence in your products and services by reducing the likelihood of failure.
Streamline Problem-Solving: Develop a structured methodology to prioritize risks and focus on what matters most.
Meet Industry Standards: Comply with quality frameworks like APQP, PPAP, AIAG 2019, and AS9145 for automotive and aerospace sectors.
FMEA enables teams to move from reactive firefighting to proactive problem prevention, fostering a culture of continuous improvement and reliability.
Course Overview
At Next Level Performance, our FMEA course equips teams with the tools, techniques, and mindset needed to integrate risk analysis seamlessly into their workflows. This course is ideal for quality engineers, design teams, and manufacturing professionals who aim to drive excellence and resilience in their operations.
Course Content
Our comprehensive course includes:
Introduction to FMEA:
What is FMEA, and why is it essential?
The evolution of FMEA: From traditional models to AIAG & VDA standards for automotive and AS9145 for aerospace.
Meeting the requirements of AIAG’s 2019 FMEA Handbook.
Types of FMEA:
Design FMEA (DFMEA): Identifying risks in product design.
Process FMEA (PFMEA): Addressing potential failures in manufacturing processes.
System FMEA: Evaluating risks across complex systems.
FMEA Methodology:
Understanding the FMEA process flow.
Key elements: Severity, Occurrence, Detection, and Risk Priority Number (RPN).
Transitioning to Action Priority (AP) for more effective risk prioritization.
Developing an Effective FMEA:
Techniques for cross-functional team collaboration.
Identifying potential failure modes and their effects.
Strategies for defining and implementing corrective actions.
FMEA Tools and Templates:
Leveraging standardized templates and digital tools to streamline the process.
Integrating FMEA into APQP and PPAP frameworks.
Ensuring compliance with AIAG 2019 standards.
Real-World Applications and Case Studies:
Practical exercises to apply FMEA principles to real-world scenarios.
Success stories from industries including automotive, aerospace, and manufacturing.
Key Takeaways
Participants will leave the course with the ability to:
Conduct comprehensive FMEA studies to identify and mitigate risks effectively.
Prioritize risks and implement corrective actions for high-impact areas.
Leverage FMEA as a continuous improvement tool.
Align FMEA practices with industry standards like AIAG 2019, VDA, and AS9145.
Who Should Attend?
This course is designed for:
Quality professionals and engineers.
Design and manufacturing teams.
Process owners and supervisors.
Leaders committed to driving a proactive risk management culture.
Invest in Proactive Quality Today
Don’t wait for problems to arise—take control with FMEA. Equip your team with the expertise to identify risks early, improve reliability, and exceed customer expectations.
Contact us today to learn more or book your training session.