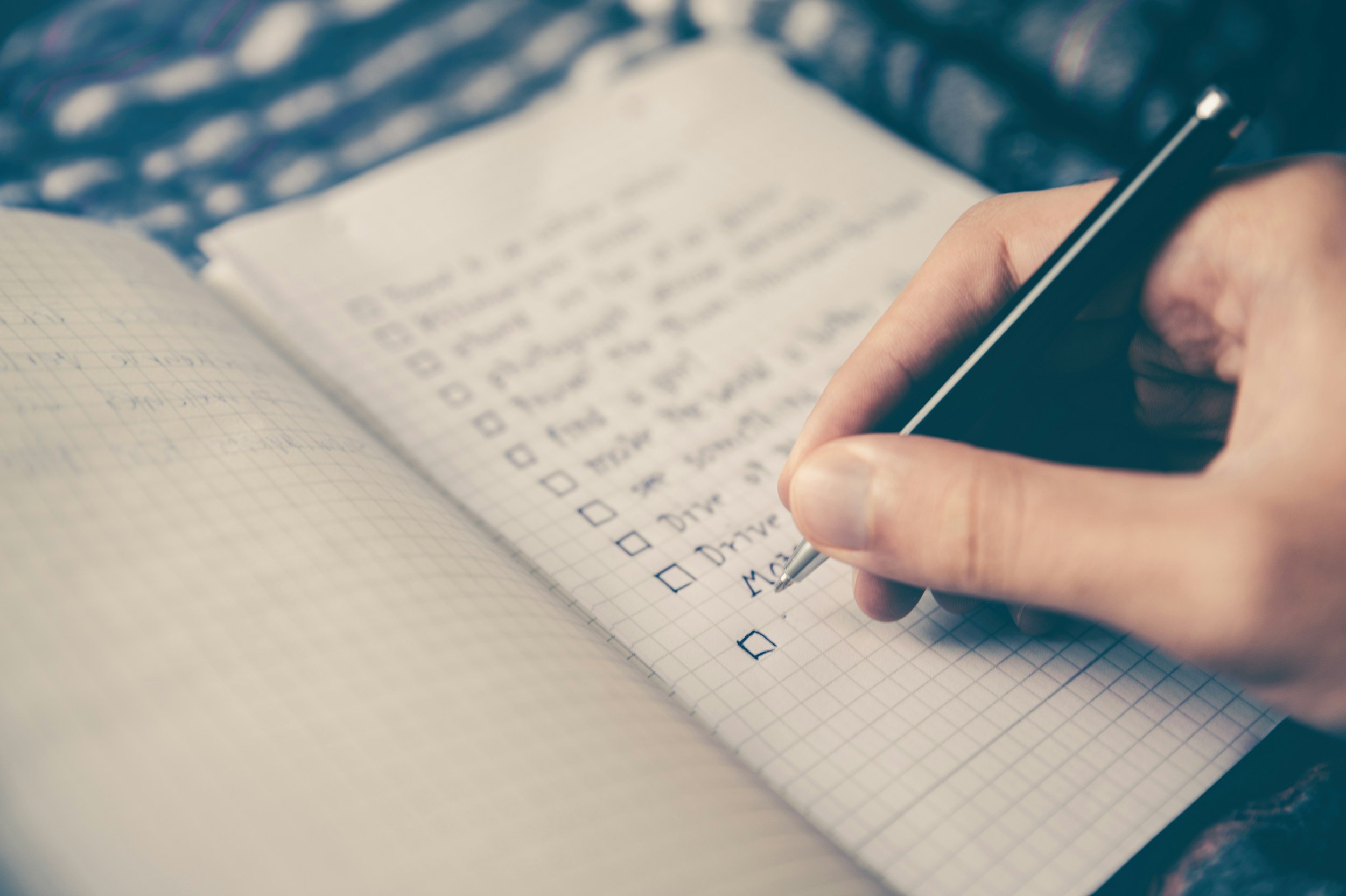
APQP (Advanced Product Quality Planning)
PPAP (Production Part Approval Process)
Quality Core Tools
Why APQP and PPAP Matter for Your Organization
In a world where quality isn’t just an expectation but a baseline, Advanced Product Quality Planning (APQP) and Production Part Approval Process (PPAP) aren’t just tools—they're your edge. They're how you turn promises into products that work, every time.
Here’s the thing: most companies wait until the end to solve problems. But with APQP, you’re starting at the beginning, designing a process that builds quality into every step. It’s about anticipating issues before they become expensive mistakes. It’s the difference between hoping it works and knowing it will.
And then there’s PPAP. Think of it as your guarantee—not just to your customer, but to yourself. It says, “This part is ready. We’ve tested it. We’ve proven it. And we can do it again tomorrow.” It’s not about compliance—it’s about confidence.
APQP and PPAP don’t just prevent failure—they pave the way for success. They help you build trust, deliver on your promises, and set you apart in a market where everyone else is just “good enough.” They show that you’re not cutting corners, you’re building a foundation.
Because in the end, quality isn’t an accident—it’s a choice. And the organizations that embrace APQP and PPAP are choosing to lead, not follow.
Course Content -
Can also be tailored depending on skills and experience.
1. Introduction to APQP and PPAP
Understanding APQP: Overview of the Advanced Product Quality Planning framework and its role in managing product development and quality planning.
What is PPAP?: Comprehensive look at the Production Part Approval Process, how it fits into the product lifecycle, and why it’s critical for customer approval.
2. APQP: Five Phases of Quality Planning
Phase 1: Planning & Defining the Program
Aligning customer requirements with internal processes.
Defining project objectives, timelines, and goals.
Phase 2: Product Design and Development
Conducting Design Failure Mode and Effect Analysis (DFMEA).
Design validation, reviews, and prototype testing.
Phase 3: Process Design and Development
Process flowcharts, Process Failure Mode and Effect Analysis (PFMEA), and Control Plans.
Phase 4: Product and Process Validation
Pre-production trial runs and validation.
Measurement System Analysis (MSA) and Statistical Process Control (SPC) studies.
Phase 5: Continuous Feedback & Corrective Actions
Implementing continuous feedback loops.
Addressing corrective actions to improve future production runs.
3. PPAP: Ensuring Production Readiness
The 18 Key Elements of PPAP: In-depth coverage of each element, including design records, process flows, control plans, and process capability studies.
Preparing PPAP Documentation: How to create, submit, and manage the Part Submission Warrant (PSW) and supporting documents for customer approval.
4. Key Tools and Techniques
Risk Management Tools: Using DFMEA and PFMEA to identify and mitigate risks early in the design and production processes.
Statistical Analysis: Conducting Measurement System Analysis (MSA) and Statistical Process Control (SPC) to ensure process capability and quality.
Control Plans: Developing and maintaining control plans to ensure consistent, repeatable production quality.
5. Deployment & Integration into Organizational Culture
Sustainable Implementation: Strategies to embed APQP and PPAP into the organizational culture, ensuring they become part of everyday operations.
Cross-Functional Teams: Training on how to build and manage cross-functional teams to improve communication and collaboration between departments.
Leadership and Continuous Improvement: How leaders can drive continuous improvement efforts and foster a culture that supports APQP and PPAP practices.
6. Real-World Applications
Case Studies: Real-life examples of successful APQP and PPAP implementations in various industries.
Hands-On Exercises: Practical workshops that simulate real-world scenarios, allowing participants to practice creating control plans, conducting PFMEA, and preparing PPAP documentation.
7. Sustaining Results
Best Practices: Insights on how to sustain the benefits of APQP and PPAP through ongoing audits, performance reviews, and continuous improvement initiatives.
Training Outcomes
Participants will leave the training with:
A comprehensive understanding of APQP and PPAP processes.
The ability to develop and implement control plans, DFMEA/PFMEA, and process validation methods.
Skills to integrate these quality planning processes into their organizational culture to ensure long-term success.
Practical experience preparing PPAP submissions and engaging with customers during the approval process.