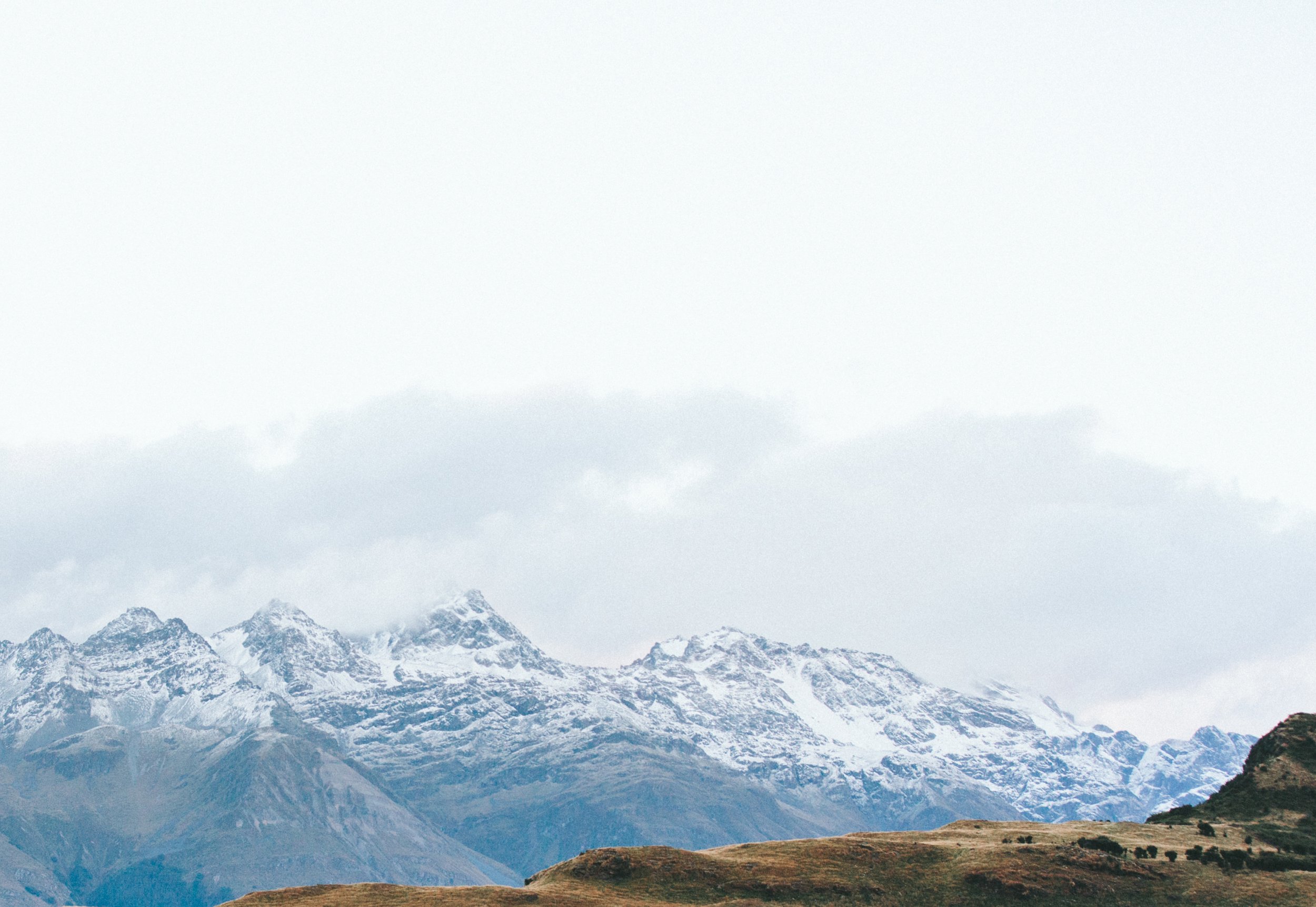
Lean Six Sigma Training Course & Implementation Guide.
We have seen clients benefit most when the tools are hand-select which are tailored to their unique business needs which is then supported by providing the learning culture.
Lean Tools
Mix & Match available depending on your needs
We can Perform a Lean Assessment which will help to define which tools would benefit you.
Introduction to Lean (management and shop floor)
5S (Fantastic foundation for all manufacturing activities)
Problem solving
Lean Deployment
The 7 waste of Lean.
SMED (Single Minute Exchange of Die)
Visual Management
Kiazen
Total Preventative Maintenance
Production Lead Maintenance
Value Stream Mapping
Mistake Proofing
Yellow Belt
Mix & Match available depending on your needs.
Introduction to Six Sigma
Sigma Rating
DMAIC
Project selection / Charter
Voice of the Customer
Cost Of Poor Quality
Teamworking
Standard Operating Procedures
Process & Value stream mapping
Cycle time reduction
Attribute & Variable Data
Data collection & Sampling
Data validity & Reliability
SPC, & Capability
Stratification
Histograms & Distribution
Pareto Analysis
Brain storming - Cause & effect
Basic FMEA
Six Sigma Tools
Mix & Match available depending on your needs
Lean -Six Sigma Strategy, Deployment & Culture.
(1 day)
Lean-Six Sigma Belts
Yellow Belt (3 Days)
Learn Basic problem solving tools
Green Belt (10 Days)
Serious about Problem solving.
Black Belt (15 days)
The ultimate Problem solver
Green Belt
Mix & Match available depending on your needs.
Yellow Belt +
Problem statement + Goal statement + Project Charter
Kano Analysis
Critical To Quality
SIPCO
OEE (Overall equipment effectiveness)
Statistic
Data Collection
Sampling Strategy
MSA (Measurement System Analysis)
Process Capability
Capability analysis
Long and Short Term Capability
FMEA (Failure Mode Effect Analysis)
PPM / DPMO /
DoE (Design of experiments)
VSM (Value Stream Mapping)
7 Wastes
Visual Management
Kanban
Triple 5 why’s
Cause and effect
Pareto Analysis
Hypothesis testing
Weibull Right Centred Reliability Analysis
6 panel / A3 / 8D principles
Error proofing
Control Charts (SPC)
Black Belts Please Contact Us to make sure we can tailor to your needs
Learning Outcome, Implementation & Support.
Empowering Delegates to Drive Business Success.
Our training equips delegates with the skills and mindset to directly contribute to the overall goals and success of their organization. When individuals understand the why behind their actions and how they contribute to the bigger picture, the likelihood of success significantly increases. Delegates will be able to demonstrate tangible financial savings that directly impact the bottom line.
Through our program, delegates develop a logical and structured approach to problem-solving using the DMAIC-R framework (Define, Measure, Analyze, Improve, Control – Replicate). This simple yet effective process ensures that problems are resolved in a robust and sustainable manner. Additionally, participants gain hands-on experience managing projects and collaborating with stakeholders, which builds their confidence and leadership abilities.
Training Outcomes
As a training provider, we believe in driving real behavioural change. Upon completion, your workforce will:
Make Data-Driven Decisions: Key decisions will be grounded in data, leading to more accurate and informed business outcomes.
Request Evidence to Support Hypotheses: Delegates will develop the habit of requesting relevant data to validate information and support decision-making.
Employ a Methodical Problem-Solving Approach: Using DMAIC-R, they will tackle problems with data-first, avoiding hasty corrective actions and ensuring deeper understanding before implementing solutions.
Lead Cross-Functional Problem-Solving Teams: Delegates will demonstrate the ability to lead collaborative problem-solving activities, leveraging input from various departments to drive meaningful results.
Continuously Seek Improvement Opportunities: With a continuous improvement mindset, they will actively identify areas to enhance processes and performance.
Manage Projects from Start to Finish: Delegates will confidently oversee projects, ensuring timelines, budgets, and goals are consistently met.
Communicate Complex Data Effectively: They will present data and findings in a clear, concise manner, gaining buy-in from leadership and team members alike.
Navigate Change and Resistance: Delegates will manage resistance to change with ease, ensuring that improvements are embraced and sustained across the organization.
Coaching
Throughout the project, we integrate personalized coaching opportunities through face-to-face interactions, video conferencing, phone calls, and email support. Our trainers have first-hand experience in your role and understand the unique pressures, challenges, and internal dynamics you face—such as overcoming roadblocks, navigating organizational politics, and balancing daily responsibilities—while still driving project savings and delivering results.
We offer hands-on support to help your business implement Lean Six Sigma tools and foster a culture of continuous improvement, driving sustainable change and measurable results